A la une

Les composites à matrice céramique (CMC) ont émergé au début des années 1970 dans un contexte d'innovations technologiques majeures pour la défense et le spatial. Initialement, ces matériaux servaient de composants pour les moteurs de fusée et de boucliers thermiques pour les rentrées atmosphériques. Rappelez-vous du film Apollo XIII ! Rapidement, leur utilisation s'est étendue à l’aéronautique militaire, puis civile. Parallèlement, ils ont été testés pour la production d’énergie dans les turbines à gaz et les centrales nucléaires.
Aujourd'hui, leurs propriétés exceptionnelles les ont propulsés dans le transport terrestre, l’industrie, et même le génie civil avancé. Qu'il s'agisse d'applications de courte durée à ultra-haute température ou de longue durée à des températures modérées, les CMC résistent et performent
Un peu de chimie pour les composites à matrice céramique
L’origine de ces matériaux remonte au développement des fibres haute performance comme la fibre de carbone. Leur dispersion dans des matrices organiques (polymères ou époxy) a permis de créer des matériaux composites ultra performants et légers que l’on retrouve dans de très nombreux objets du quotidien, comme les équipements sportifs. Cependant, une matrice organique ne peut être utilisée à haute température : elle se décompose. Et s’il était possible de remplacer cette matrice organique par… du carbone ? par exemple, en la pyrolysant ? C’est ainsi que sont nés les premiers CMC : des composites carbone/carbone très légers, très résistants aux chocs thermiques, utilisés comme cols de tuyère de fusées.

La sensibilité du carbone à l’oxydation a cependant limité leurs applications. Pour contourner cet obstacle, des matrices en carbure de silicium, qui se recouvre spontanément de verre de silice protecteur, ont été mises au point. Des fibres en carbure de silicium ont également été développées, bien plus rigides que l’acier et résistant à 1 300 °C. D’autres matériaux réfractaires comme les oxydes ont aussi été étudiés. En quelques années, la grande famille des CMC était née et offre encore aujourd’hui un terrain de jeu sans frontières pour une recherche à l’interface entre chimie, physique et ingénierie.
De la fibre au matériau composite : une histoire d’interfaces
Ce qui fait qu’un CMC est bien supérieur à une céramique réfractaire de même composition est son architecture, qui lui confère une fragilité bien moindre. En effet, la résistance à la fissuration est le talon d’Achille des céramiques traditionnelles : une fois la fissure créée, rien n’arrête sa propagation. Dans un CMC, si l’on choisit judicieusement la façon dont la fibre et la matrice sont reliées, une fissure dans la matrice n’entraîne plus automatiquement la rupture des fibres. Bien au contraire, les fibres pontent la fissure et ralentissent sa propagation. Plusieurs fissures peuvent apparaître et on parle alors d’endommagement progressif.
Fabriquer un matériau tenace à partir de deux constituants fragiles : tel est le défi des CMC. Cette synergie tant recherchée repose sur le design d’une couche d’interface entre fibres et matrice qui permet de dévier la fissure et dissiper l’énergie mécanique dans le matériau. On parle de « fusible mécanique ». Un comportement qui n’est pas sans rappeler celui du bois, composite fibreux naturel connu pour sa ténacité.
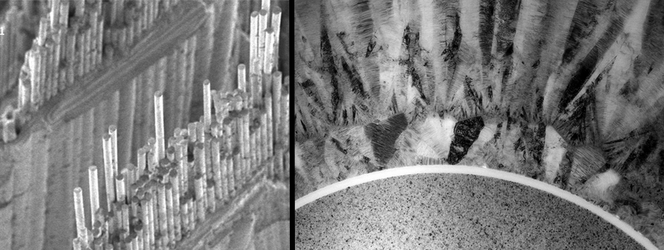
C’est donc à une toute petite échelle (inférieure au micron) que se joue la performance des CMC. Des dimensions macroscopiques au nanomètre, ces céramiques renforcées sont devenues le sujet d’intenses efforts de recherches et développements depuis les années 1960.
Petit CMC deviendra grand
Aurait-on épuisé le sujet ? Loin de là, et les perspectives de recherche et de développement sont nombreuses.
Tout d’abord, les CMC commencent enfin à être intégrés aux moteurs d’avions civils après de longs cycles de mise au point et de qualification, ce qui en augmente significativement le volume de marché. Conséquence : les coûts des matières premières et des procédés baissent, ouvrant la voie à de nouvelles applications économiquement viables, notamment dans l’industrie ou l’énergétique. Actuellement, les CMC représentent près de 10 % du chiffre d’affaires total des matériaux composites et leur croissance annuelle est de 8 à 10 % ! Cerise sur le gâteau, les CMC sont essentiellement constitués d’éléments abondants (silicium, carbone, aluminium, oxygène, azote…) et sont donc bien positionnés pour remplacer des « minéraux critiques » comme le titane ou le nickel.
Les fortes tensions géopolitiques et les conflits récents stimulent par ailleurs le développement de technologies de défense avancées. Prenons par exemple les missiles hypersoniques qui se déplacent à des vitesses largement supérieures à celle du son (Mach 5) et selon des trajectoires non prévisibles. Ils doivent en partie leurs performances aux CMC. De nouvelles familles de CMC ultra-haute température (UHTCMC) voient même le jour, qui sont composées de céramiques ultra réfractaires. Si ce thème de recherche ne fait pas la une des grands journaux, il est bel et bien en plein essor.
L’excellence et le dynamisme de la recherche française sur les CMC permet d’appuyer un tissu d’industriels qui produisent de nombreux systèmes stratégiques présents au meilleur rang dans la compétition mondiale en aéronautique et dans le spatial. Les enjeux actuels et futurs militent pour la poursuite et l’amplification de cette position. Au-delà de la souveraineté militaire et énergétique, il en va aussi de l’indépendance de l’accès à l’espace, de la désensibilisation aux « minéraux critiques », de la mutation du transport et de l’industrie en lien avec la décarbonation, etc. Dans tous ces domaines, les CMC auront leur rôle à jouer.
Le CNRS a soutenu ces recherches depuis leur genèse, d’abord par la création du Laboratoire des composites thermostructuraux1 en 1988. Plus récemment, le Groupement de Recherche Composites à matrice Céramique : Conception, Modélisation, Caractérisation (CMC)2 a vu le jour et fédère la communauté française autour de ces matériaux2. Une réflexion sur leur avenir a récemment été conduite par un groupe de travail réunissant acteurs industriels et académiques du GDR. Elle a notamment permis d’identifier des recommandations jugées essentielles pour consolider et renforcer ce secteur d’activité. Un effort de prospective très complet à retrouver dans le livre blanc des CMC3. ♦
Gérard Vignoles, professeur à l’université de Bordeaux, mène des recherches sur l’élaboration et les propriétés de matériaux composites à matrice céramique au Laboratoire des composites thermostructuraux (CNRS/Université de Bordeaux/CEA/Safran). Depuis 2019, il dirige le groupement de recherche (CMC)2.
Anne-Valérie Ruzette, chercheuse en physico-chimie des polymères, coordonne la cellule d’expertise de CNRS Chimie et conduit de nombreuses missions de diffusion des connaissances pour la chimie.
- 1. LCTS, unité CNRS/Université de Bordeaux/CEA/Safran.
- 2. https://gdr-cmc2.cnrs.fr/
- 3. https://gdr-cmc2.cnrs.fr/le-livre-blanc/