Vous êtes ici
La céramique sert à tout !
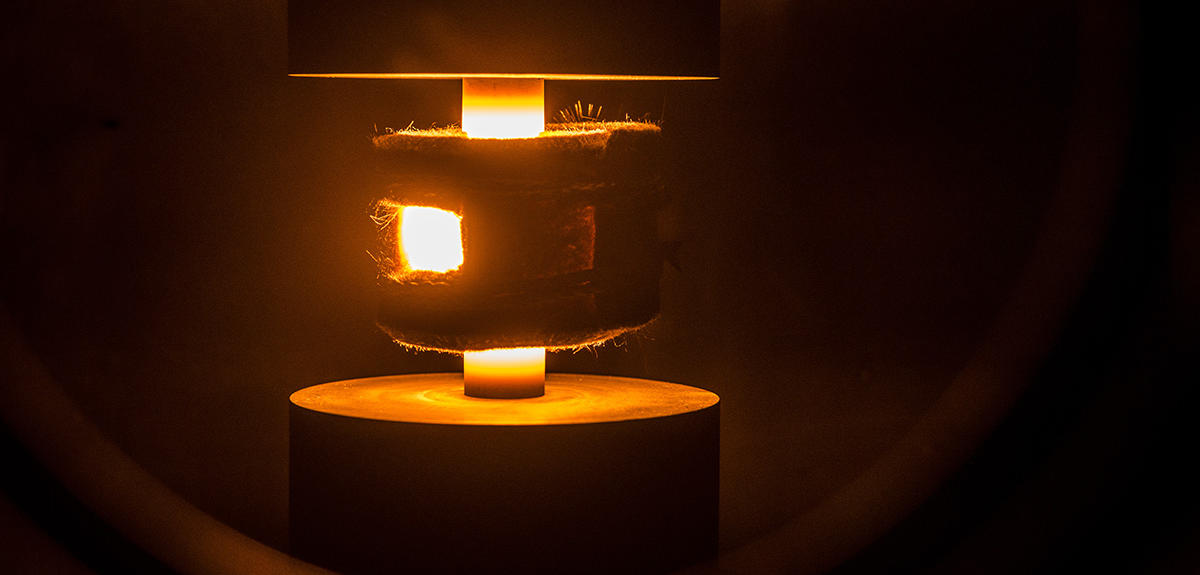
Des poteries alimentaires aux matériaux du bâtiment en passant par les plus high-tech des implants, les céramiques, connues depuis la préhistoire, sont des matériaux précieux en aéronautique, en médecine, dans les domaines de l’énergie, de l’environnement et bien d’autres encore. La recette de base, le frittage, est toujours la même : chauffer à haute température un amas de poudre pour que ses grains s’agglomèrent jusqu’à former une structure compacte, plus ou moins poreuse. Propriétés remarquables de cette microstructure : porosité, grande duretéFermerRésistance qu’oppose la surface d’un matériau à une déformation., résistance aux températures élevées, inertie chimique (c’est-à-dire stabilité par rapport à l’environnement), et même légèreté et transparence. Mais on peut faire encore mieux ! Les chercheurs se penchent donc sur la composition chimique et le contrôle de plus en plus fin de la microstructure de ces matériaux, révolutionnaires depuis l’âge de pierre…
Résistantes aux conditions extrêmes…
Comme le diamant, les céramiques sont très dures mais ont une faible ténacitéFermerRésistance aux chocs et à la propagation de fissures. : peu résistantes aux chocs, elles cassent facilement. Pour y remédier, des matériaux formés d’une matrice céramique renforcée par des fibres, elles-mêmes en céramique, ont été développés. Résultat : ces composites à matrice céramique (CMC) associent la solidité et la légèreté d’un composite à la résistance aux hautes températures d’une céramique. À Pessac, le Laboratoire des composites thermostructuraux (LCTS)1 en a fait sa spécialité. Y sont développés des matériaux, de compositions chimiques et d’architectures variées, adaptés aux conditions les plus extrêmes : températures supérieures à 1 000 °C, chocs thermiques, milieux oxydants et corrosifs…

« Les CMC débouchent actuellement sur une application industrielle majeure : ils vont pouvoir remplacer les pièces métalliques des moteurs d’avion. Deux à trois fois plus légers, plus résistants, ils amélioreront le rendement des moteurs tout en réduisant la dépense énergétique et la pollution », commente Gérard-Louis Vignoles, directeur du LCTS. Si ces matériaux investissent peu à peu le secteur industriel, les chercheurs voient plus loin. En les soumettant à des conditions intenses et variées (sollicitations mécaniques, thermiques, chimiques, tribologiques, indépendantes ou combinées), ils travaillent sur les prochaines générations de CMC qui résisteront à des températures encore plus élevées (de 1 500 à 3 000 °C). Ce type de recherches – également menées dans le cadre de programmes collaboratifs entre le CNRS et l’Onera – permettra de répondre à des besoins très spécifiques, tels que la rentrée atmosphérique des objets spatiaux. « Mais ces matériaux sont récents, nous ne disposons pas d’un retour d’expérience aussi important que pour les métaux ou les alliages. Nous devons donc élucider tous les mécanismes fondamentaux qui peuvent mener à leur baisse de performance puis à leur ruine. L’enjeu est en effet de conserver une résistance aux conditions extrêmes sur des temps très longs », précise le chercheur.
… voire incassables !
Pour les rendre encore plus tenaces, il faut agir sur la microstructure des céramiques. Des chercheurs du Laboratoire de synthèse et fonctionnalisation des céramiques (LSFC)2 de Cavaillon ont eu une idée originale : mimer la structure de la nacre qui recouvre certains coquillages. « La nacre est constituée d’un matériau fragile, le carbonate de calcium, et pourtant la structure qu’il forme est 3 000 fois plus résistante que ses briques de base », explique Sylvain Deville, chercheur au LSFC. Cette spécificité est due à l’organisation de ses composants, qui s’apparente à un empilement de petites « briques » (carbonate de calcium) soudées par un « mortier » composé de protéines. De fait, pour se propager, une fissure doit contourner chaque brique, ce qui freine sa progression. Pour reproduire cette structure, les chercheurs ont fait preuve d’une grande ingéniosité : utiliser la congélation. Concrètement, des plaquettes d’alumine (poudre céramique courante), mises en suspension dans l’eau avec un « mortier », ont été congelées de manière contrôlée ; elles se sont ainsi auto-assemblées en s’alignant et s’empilant comme le carbonate de calcium dans la nacre. Après avoir recherché la composition du « mortier » fournissant le meilleur compromis entre résistance et ténacité à la structure finale, ils ont obtenu une céramique aux effets nacrés jusqu’à dix fois plus tenace qu’une céramique classique ! Sans surcoût, les procédés de congélation pourraient s’avérer très porteurs pour la fabrication de céramiques industrielles. L’entreprise Saint-Gobain, cotutelle du laboratoire, réalise des études en ce sens.

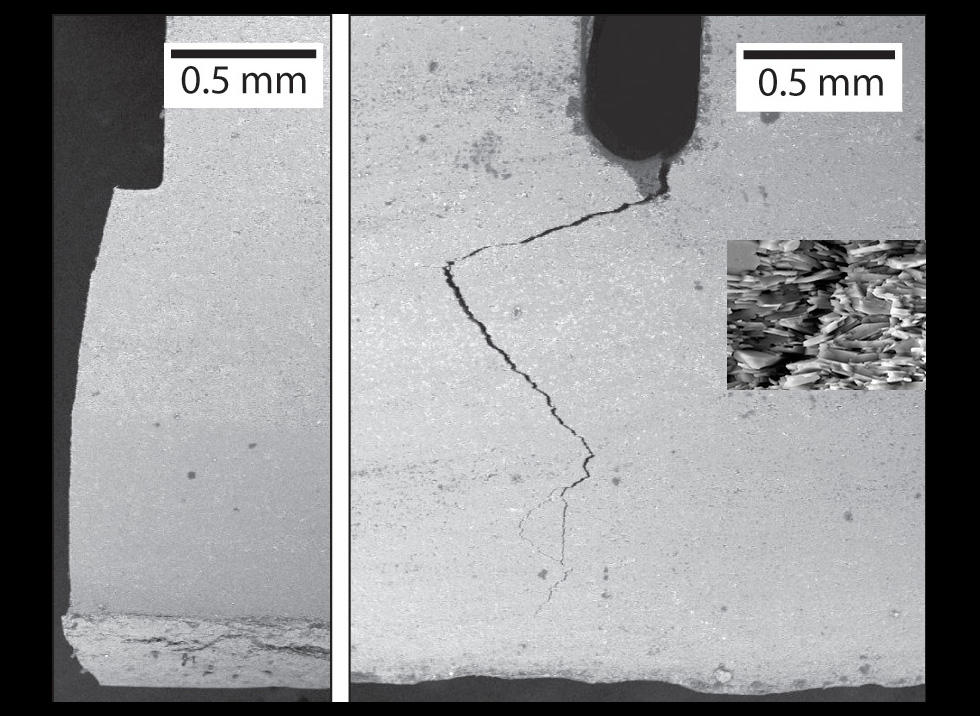
Plus de transparence
Verres de montre, blindage de fenêtre d’hélicoptère… Les céramiques, connues depuis longtemps pour leur grande résistance mécanique, devraient s’inviter dans de nouvelles applications grâce à une propriété plus récente : la transparence. Depuis une vingtaine d’années, celle-ci est obtenue en fabriquant des céramiques denses, sans porosité : la diffusion de la lumière est alors limitée et ces céramiques (matériaux isotropesFermerUn matériau isotrope se caractérise par des propriétés identiques dans toutes les directions. le plus souvent) acquièrent une transparence et des propriétés d’émission de lumière parfois égales aux qualités optiques et photoniques des monocristaux. L’absence de porosité est obtenue par frittage à haute température et haute pression de poudres souvent très fines, préalablement préparées physiquement et chimiquement.
Les chercheurs essaient aujourd’hui de rendre ces procédés moins complexes et moins coûteux, par exemple en élaborant des céramiques fluorées. Par frittage à température modérée, la technique développée par l’équipe de Michel Mortier à l’Institut de recherche de chimie Paris3, fournit un matériau polycristallin totalement dense et d’une transparence parfaite. Le procédé – breveté – et le matériau obtenu permettent d’envisager la conception de lasers pulsés à très haute puissance.
Autre piste originale : développer des matériaux polycristallins transparents par cristallisation complète du verre. Des chercheurs du laboratoire Cemhti4 du CNRS, à Orléans, élaborent ainsi des verres de composition particulière permettant d’avoir une cristallisation complète et massive. « Outre l’obtention d’un matériau sans porosité, notre approche permet un dopage (insertion d’éléments chimiques qui optimisent l’émission de lumière) homogène et repose sur la synthèse du verre, procédé simple et peu onéreux », commente Mathieu Allix, chercheur au Cemhti. Avec son équipe, il vient d’ailleurs de mettre au point des céramiques transparentes à base de YAG (grenat d’yttrium et d’aluminium), par cristallisation à pression ambiante d’un verre de même composition. En offrant un matériau aux propriétés optiques et mécaniques aussi performantes que celles des matériaux YAG habituels, cette technique simple et peu coûteuse pourrait avoir un fort impact dans les domaines de la joaillerie, des lentilles optiques et des diodes électroluminescentes.
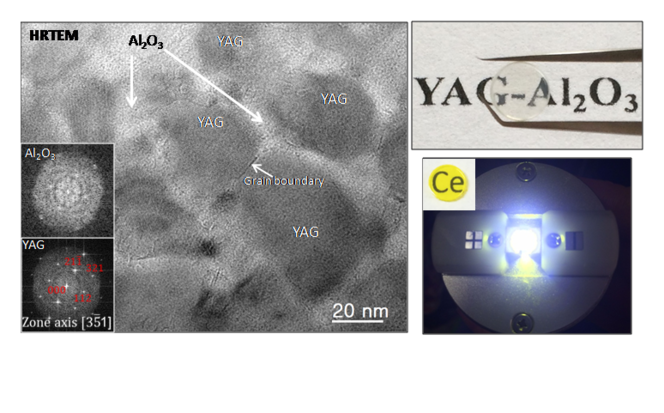
Des implants osseux éphémères
Formés de céramiques, les implants actuellement utilisés en chirurgie osseuse restent fragiles, surtout quand ils remplacent de grands volumes d’os ou sont insérés dans des zones à fortes sollicitations mécaniques, comme la mâchoire par exemple. D’où l’idée de concevoir des implants « éphémères » qui serviraient uniquement de support à la repousse de l’os jusqu’à sa régénération complète, et disparaîtraient ensuite. « La repousse osseuse est lente et limitée en volume. Notre défi est de mettre au point des implants qui la stimulent. Nous y travaillons via trois leviers : en optimisant la composition chimique de la céramique pour améliorer sa biocompatibilité et sa résorbabilité, en concevant par fabrication additiveFermerDessiné par conception assistée par ordinateur à partir d’images scanner réalisées sur le patient, l’implant est fabriqué par stéréolithographie, soit couche par couche d’environ 100 µm d’épaisseur. des implants sur mesure dotés d’une porosité favorisant l’invasion des cellules osseuses, et enfin en intégrant dans la céramique du matériel biologique, comme des protéines stimulatrices de la croissance cellulaire », explique Éric Champion, chercheur à l’Institut de recherche sur les céramiques (Ircer)5, à Limoges. Les chercheurs de l’Ircer se concentrent en particulier sur la formation des vaisseaux sanguins, indispensables au développement du tissu osseux. Ils ont ainsi montré que des pores de forme triangulaire, plutôt que circulaire, permettent un meilleur guidage des vaisseaux dans l’implant. Une telle génération d’implants permettrait de faire face au nombre croissant de situations nécessitant une restauration osseuse, qu’il s’agisse de lésions accidentelles, cancéreuses ou de pathologies du vieillissement.

Une porosité utile pour l’environnement
Poreuses par nature, les céramiques permettent de filtrer et traiter les liquides et les gaz. Le plus souvent formées d’oxydes ou de non-oxydes, elles sont ainsi utilisées dans de nombreuses applications, comme la décontamination bactérienne de l’eau ou la dépollution des gaz d’échappement.
« Outre le fait qu’ils résistent mieux et plus longtemps que les filtres polymères à des conditions d’utilisation sévères, les filtres faits de céramique permettent d’atteindre des niveaux de filtration très fins (de quelques nanomètres à quelques angströmsFermerUn angström équivaut à 0,1 nanomètre, soit 10−10 mètre (un dixième de milliardième de mètre).) et peuvent aussi servir de support à des réactions chimiques permettant d’éliminer des particules ou molécules indésirables (fonctions catalytiques) », explique Anne Julbe, chercheuse à l’Institut européen des membranes (IEM)6, à Montpellier. La mise au point de ces filtres requiert une véritable ingénierie du matériau et, particulièrement, un contrôle fin de la porosité et de la microstructure des pores (tailles, connexions, distributions…), mais également des propriétés de la surface (composition, charge électrique…). De ces deux paramètres dépendent la sélectivité du filtre vis-à-vis des espèces visées et l’activité catalytique qui peut lui être attribuée.

« Notre défi est de développer des filtres capables de cibler des espèces de plus en plus petites (des molécules de gaz de quelques angströms, par exemple) ou présentes en très faibles concentrations (des micropolluants tels que les perturbateurs endocriniens). Cela impose aussi de mettre au point des techniques permettant d’analyser leurs performances à de telles échelles », précise André Ayral, chercheur à l’IEM. Le laboratoire développe notamment des membranes de séparation des gaz, par exemple pour isoler l’hydrogène, matière première la plus utilisée dans les piles à combustible. Ou encore des membranes catalytiques qui combinent filtration et dégradation d’espèces nocives par des réactions d’oxydation (photocatalyse ou ozonation catalytique). De tels filtres, conçus via des procédés économes et durables, garantiront un meilleur contrôle des rejets industriels et urbains (eaux usées traitées, par exemple) dans le milieu naturel.
De futurs réacteurs nucléaires
Les pastilles d’oxyde d’uranium, combustibles des réacteurs nucléaires, sont en fait des céramiques. Elles fournissent ainsi un matériau résistant aux conditions extrêmes du milieu : températures (plus de 300 °C), pression (150 fois la pression atmosphérique), irradiation. Préparer la quatrième génération de réacteurs (réacteur à neutrons rapides notamment) et répondre à leurs enjeux – réutilisation d’une partie des déchets, amélioration de leur sécurité… – impose aujourd’hui de faire évoluer ces matériaux combustibles.
Des chercheurs s’emploient déjà à prévoir leurs nouvelles propriétés (introduction de nouveaux éléments chimiques, résistance à des températures et des flux de neutrons plus élevés…). À l’Institut de chimie séparative de Marcoule (ICSM)7, ils tentent notamment de contrôler de manière optimale la microstructure des combustibles grâce à un dispositif d’observation inédit qui permet, via une technique de microscopie électronique8, de suivre en temps réel la formation de la microstructure.
« Par cette approche, nous accédons expérimentalement aux phénomènes fondamentaux qui régissent le frittage. Les données obtenues permettent d’améliorer les modèles de simulation dynamique de la microstructure, en les rendant plus fidèles à la réalité. Au final, nous disposons de modèles capables de prédire de manière de plus en plus fiable la microstructure des combustibles et son évolution », explique Nicolas Clavier, chercheur à l’ICSM. Des modèles indispensables pour anticiper le comportement des futurs combustibles.
À l’autre bout du cycle du combustible, des travaux sont également menés pour concevoir des céramiques adaptées au confinement de certains déchets. Inspirées de minéraux naturellement résistants à la radioactivité, ces céramiques pourraient répondre aux enjeux de certains modes de retraitement envisagés, comme l’enfouissement sur de très longues durées (projet Cigéo). ♦
- 1. Unité CNRS/Université de Bordeaux/Safran/CEA.
- 2. Unité CNRS/Saint-Gobain.
- 3. Unité CNRS/Chimie ParisTech.
- 4. Conditions extrêmes et matériaux : haute température et irradiation.
- 5. Unité CNRS/Université de Limoges/ENSCI.
- 6. Unité CNRS/ENSCM/Université de Montpellier.
- 7. Unité CNRS/CEA/Université de Montpellier/ENSCM.
- 8. Technique de microscopie électronique à balayage en mode environnemental à haute température.
Voir aussi
Auteur
Rédactrice scientifique depuis plus de dix ans, Stéphanie Belaud s’est notamment spécialisée dans les domaines de la biologie, de la médecine et de l’environnement.