Vous êtes ici
Avion : la quête du moteur idéal
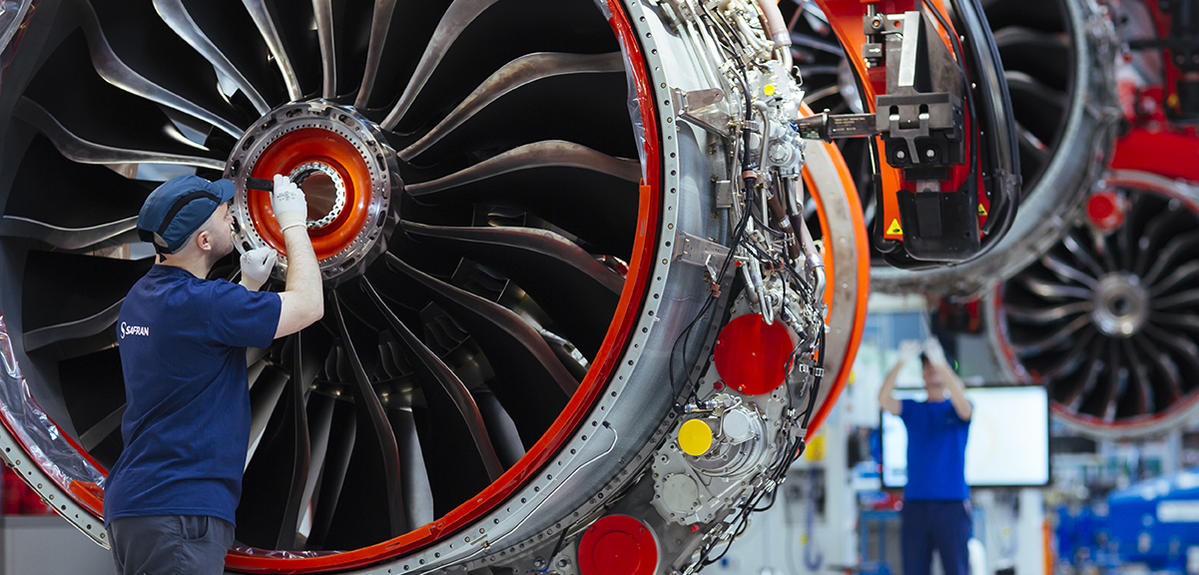
Pour fendre les cieux, il faut savoir s’appuyer sur l’air. Et sans une propulsion efficace, la portance n’est rien. Symbole de ce couplage essentiel, les avions civils affichent sous leurs ailes d’imposants moteurs à réaction. Ceux-ci sont le théâtre de phénomènes complexes que les scientifiques veulent toujours plus maîtriser et optimiser. Dans ce domaine, le CNRS a tissé un partenariat efficace avec l’industrie. Tant et si bien que le groupe Safran, qui a connu le plus grand succès commercial de l’aviation civile avec son célèbre CFM56, enregistre déjà 11 500 commandes pour son nouveau moteur LEAP, aboutissement de recherches de longue haleine.
« Le LEAP a été conçu comme le CFM56 en partenariat avec General Electric. Il est le fruit d’avancées technologiques portant sur chaque élément du moteur », indique Sébastien Candel, du Laboratoire d’énergétique moléculaire et macroscopique, combustion1 (EM2C), à Châtenay-Malabry. « Parmi ces éléments, la chambre de combustion joue un rôle majeur, poursuit le chercheur. C’est elle qui fournit à bord de l’appareil toute l’énergie nécessaire au vol : l’énergie issue de la combustion du kérosène et de l’air est transformée en énergie mécanique pour la propulsion et en énergie électrique pour les systèmes de commande de vol et pour ceux qui assurent le confort des passagers. »
Petite, mais complexe
Pourtant, la chambre de combustion ne représente qu’une toute petite partie des imposants turboréacteurs. Elle prend la forme d’un foyer annulaire proche de la taille d’une roue de voiture. Rien à voir, toutefois, avec la chambre de combustion des moteurs à explosion qui équipent nos automobiles : « À l’inverse d’un moteur à explosion où la combustion se fait de façon cyclique avec un allumage à chaque cycle, celle d’un turboréacteur doit être assurée en permanence. C’est un problème complexe car la flamme doit être stabilisée dans un écoulement à grande vitesse », explique Sébastien Candel. Pour ce faire, les chercheurs et les industriels n’ont eu de cesse de rendre la solution de plus en plus élégante et performante : « Pour nous, l’objectif est double : assurer à la fois la stabilité de la flamme et une combustion la plus complète possible avec les émissions de polluants les plus réduites », souligne-t-il.
À cette fin, la chambre de combustion possède une géométrie particulière : « D'une part, la multi-perforation des parois permet d’assurer la tenue de la chambre malgré les très hautes températures qui existent dans la zone de combustion. D’autre part, la combustion est induite par un grand nombre d’injecteurs aérodynamiques qui alimentent la chambre en kérosène et en air. Au moyen de plusieurs vrilles, le flux d’air entraîne avec lui le nuage de gouttelettes de kérosène. Cette rotation de l’écoulement induit une zone dans laquelle les gaz chauds de la combustion sont mis en recirculation afin d’initier en continu la combustion du mélange frais issu de l'injecteur », précise le physicien. L’énergie thermique ainsi produite est alors transformée en énergie mécanique au moyen d’une turbine couplée au compresseur et à la soufflanteFermerElle est le seul élément visible d'un moteur pour les passagers d’un vol commercial. Positionnées à l’avant du réacteur, ses larges pales en rotation aspirent l’air ambiant et l’envoient dans le réacteur pour générer la poussée.. Au final, c’est l’éjection des gaz en sortie de réacteur via la tuyèreFermerLa tuyère d’échappement est la partie arrière d'un réacteur d'avion. Elle permet de détendre les gaz de combustion. Ce faisant, elle contribue à transformer l’énergie thermique en énergie cinétique, autrement dit en propulsion. Sur les fusées, leurs imposantes silhouettes coniques d’où s'échappe le combustible en flamme sont particulièrement visibles. qui induit la force de propulsion : leur expulsion vers l’arrière se traduit alors en une poussée vers l’avant pour l’avion.
Le principe de la « propulsion à réaction » est en fait connu depuis… Issac Newton (1643-1727) et sa troisième loi dite d’action-réaction. Celle-ci permet en effet de montrer que la force propulsive est directement reliée au débit-masseFermerC’est la masse de fluide écoulé par unité de temps. Il se mesure en général en tonnes (ou kilogrammes) par heure (ou par seconde). du moteur et à la différence entre la vitesse des gaz éjectés et la vitesse de l’air en amont du moteur (la vitesse de l’avion). C’est aussi un Anglais, sir Frank Whittle, qui au début des années 1930, ayant compris qu’il fallait comprimer le flux d’air pour tirer un travail à partir du cycle moteur et obtenir la force de propulsion, avait donné corps au premier turboréacteur : « Depuis les premiers brevets de Franck Whittle, la technologie a beaucoup évolué, souligne Sébastien Candel, et une distance énorme sépare son travail des architectures actuelles. »
Combustion in vitro et in silico
Cette complexité grandissante des turboréacteurs a été rendue possible par une maîtrise accrue de l’aérodynamique interne, de la mécanique, des matériaux et, bien sûr, de la combustion. Et cet « art du feu », Sébastien Candel et ses collègues d’EM2C en ont acquis une connaissance théorique et pratique qui les place au meilleur niveau international. En premier lieu, grâce à un banc expérimental unique en son genre : un foyer annulaire aux parois en quartz, dénommé MICCA, mimant une petite chambre de combustion d’un réacteur. Sa particularité : là où les matériaux employés pour les réacteurs d’avion sont opaques, le quartz laisse passer la lumière : « On peut ainsi observer la dynamique de combustion, analyser au moyen d’essais l’allumage circulaire du foyer à partir de l’étincelle d’une bougie, déterminer les mécanismes qui conduisent au couplage entre la combustion et les modes acoustiques du système, explique Sébastien Candel. Le système est idéalisé mais il nous permet de réaliser des avancées importantes, notamment sur la question des instabilités de combustion. »
Ces instabilités sont les ennemis des chercheurs et des industriels : « Les améliorations récentes des turboréacteurs se sont faites au prix d’une combustion plus sensible aux phénomènes d’instabilité qu’il faut donc savoir maîtriser », précise Sébastien Candel. La force de son laboratoire est de pouvoir coupler l’expérimentation, la théorie et la simulation numérique au moyen du calcul à haute performance. Et les progrès dans ce domaine sont « fantastiques » : « On est à présent capable de simuler avec une bonne précision ce qui se passe à l’intérieur de la chambre de combustion au moment de l’allumage du foyer. Et la concordance entre les simulations et les observations est même surprenante », se félicite-t-il.
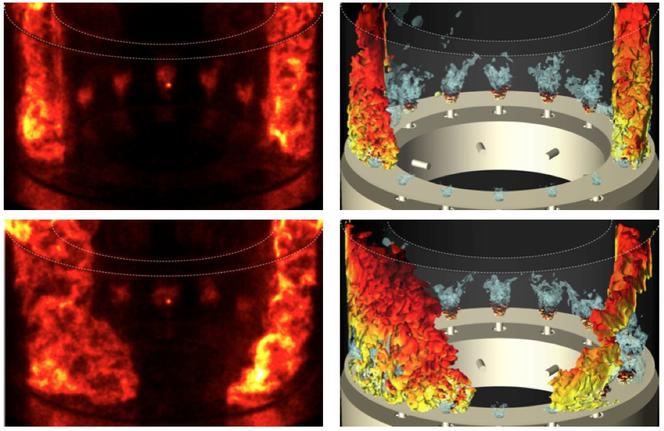
Ces avancées numériques profitent aussi aux ingénieurs. Le logiciel de simulation aux grandes échelles, AVBP, développé par l’équipe de Thierry Poinsot du Cerfacs2 de l’IMFT3 à Toulouse, et les modèles élaborés dans les laboratoires du CNRS sont ainsi directement partagés avec les ingénieurs de Safran. Cette boîte à outil est un atout pour relever les défis à venir : « Grâce à des avancées scientifiques et technologiques, l’industrie a réussi à réduire d’un facteur deux la consommation de kérosène des moteurs. Il faut compter aujourd’hui un peu plus de quatre litres par passager transporté et par 100 kilomètres, soit un ordre de grandeur comparable à celui d’une automobile. Or, le passager vole à 900 kilomètres/heure. Mais on peut encore progresser, notamment pour réduire les émissions de dioxyde d’azote et de particules de suie », évoque Sébastien Candel.
Plus gros mais moins bruyant
Même si Safran et Airbus ont annoncé en 2011 le lancement de recherches sur des moteurs hybrides alliant combustion et énergie électrique, il demeure pour le moment difficile de changer de paradigme : « L’énergie obtenue par kilogramme de kérosène est environ 40 fois plus élevée que celle qui est stockée dans un kilogramme des meilleures batteries et, même en tenant compte du rendement thermodynamique, il reste un facteur 15 entre les deux », prévient Sébastien Candel. Pour remplacer les 240 tonnes de kérosène d’un A380, il faudrait ainsi 3 600 tonnes de batteries. Et l’amélioration du rapport puissance-poids est l’objectif premier des motoristes et des avionneurs. Les imposants turboréacteurs double flux, qui sont devenus la norme dans l’aviation civile, sont de ce point de vue remarquables et ils semblent donc avoir encore de beaux jours devant eux. D’autant que l’utilisation d’un double flux d’air en entrée couplé à l’augmentation du diamètre de la soufflante a permis d’améliorer le rendement, de diminuer la consommation et d’atténuer le bruit d’éjection en sortie de réacteur.
À chaque décollage, les habitants situés à proximité des aéroports ont ainsi pu constater une réduction « de plusieurs dizaines de décibels au cours des trente dernières années », indique Daniel Juvé, directeur du Centre lyonnais d’acoustique, laboratoire d’excellence. Mais le passage aux réacteurs double flux n’est pas la seule explication. Les travaux de Daniel Juvé et de ses collègues du Laboratoire de mécanique des fluides et d’acoustique4 (LMFA) y ont également contribué. « La question clé désormais est de savoir si l’on pourra encore baisser significativement ce bruit ou si l’on approche d’un plafond de verre pour ces types de motorisation », précise-t-il. Une réponse d’autant plus attendue que la réglementation internationale sur les nuisances sonores va continuer à se durcir. De nouvelles architectures d’avion, avec des moteurs implantés au-dessus des ailes par exemple, ou de façon plus prospective, de type « aile volante », sont d’ailleurs étudiées à la fois par les chercheurs et les industriels.
Cartographie des bruits
Pour mieux cerner les sources de bruit des réacteurs, le LMFA s’est équipé d’un impressionnant banc d’essai pour l’étude des performances aérodynamiques et du bruit des soufflantes de réacteurs (Equipex Phare). Une maquette à l’échelle 1/3 d’une soufflante (la partie amont du moteur, qui est la plus bruyante) est ainsi installée dans une chambre sourde. Cette dernière permet de mesurer les sons émis sans que ceux-ci ne soit réfléchis par les parois et sans que le bruit extérieur ne vienne troubler la mesure : « En son sein, des réseaux de plusieurs centaines de microphones permettent alors de localiser les différentes sources du bruit », décrit Daniel Juvé. La chaire industrielle ADOPSYS, cofinancée par l’Agence nationale de la recherche et le groupe Safran, a permis de doter le laboratoire de nouveaux équipements encore plus performants, couplant mesures multi-microphoniques et caractérisation des écoulements par des méthodes optiques.
Car pour cartographier au mieux les sources de nuisance, les chercheurs doivent associer l’acoustique à la mécanique des fluides dans leurs mesures et leurs calculs. « Les nacelles des turboréacteurs deviennent de plus en plus grosses et l’interaction entre les jets propulsifs et la voilure augmente, multipliant les sources de bruit », explique Daniel Juvé. « Grâce aux essais en chambre sourde et aux simulations numériques intensives, nous sommes toutefois parvenus à mieux comprendre les phénomènes aéroacoustiques à l’œuvre et à proposer des solutions pour la réduction des bruits », se réjouit-il.
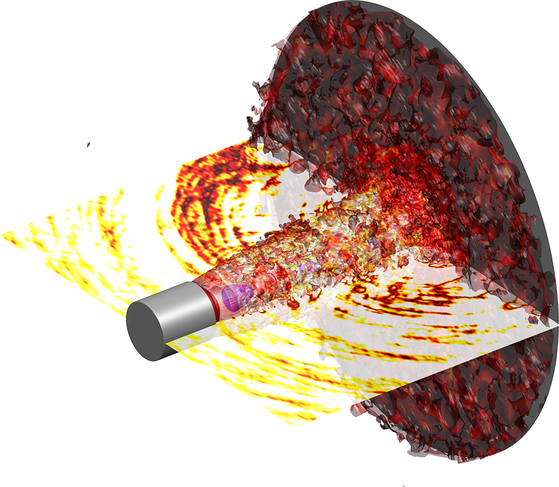
Des « pièges sonores »
Ces solutions, le Laboratoire acoustique de l’université du Maine5 les connaît mieux que personne. « L’idée est simple : une fois les sources identifiées, on cherche à les neutraliser », indique Yves Auregan. La solution phare consiste à placer autant de « pièges sonores » possibles à proximité des sources de bruit du moteur. En premier lieu, un jeu de parois perforées d’une myriade de petits trous au-dessus d’une structure en nid-d’abeilles. Chaque petit trou joue alors le rôle d’un résonateur de HelmholtzFermerSi vous avez déjà soufflé dans le haut d’une bouteille vide, vous connaissez le principe de ce dispositif créé dans les années 1850 par le scientifique allemand Hermann von Helmholtz (1821-1894). Ce dernier fut le premier à formaliser ce phénomène de résonance de l’air dans une cavité. Un principe aujourd’hui utilisé aussi bien dans les voitures ou les avions que dans les instruments de musique., piégeant les fréquences sonores ciblées. Mais cette approche atteint désormais ses limites : « L’évolution vers des moteurs de diamètre de plus en plus grand s’accompagne d’une augmentation de bruits plus bas en fréquence, plus difficiles à atténuer. En parallèle, les contraintes imposées sur la taille des nacelles ne permettent plus d’augmenter l’épaisseur des structures en nid-d’abeilles », souligne le chercheur.
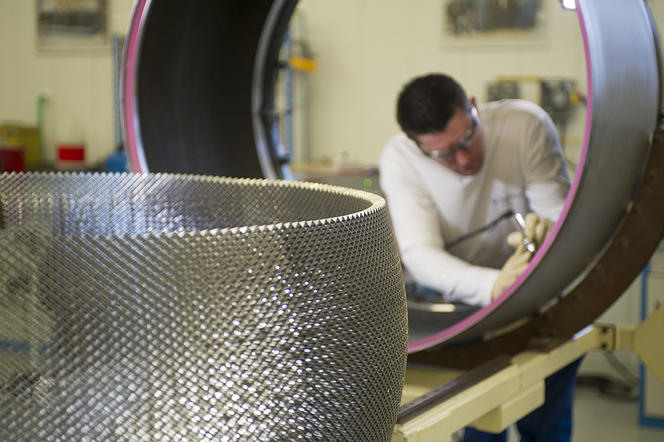
Face à cette impasse, le laboratoire d’Yves Auregan s’est associé au groupe Safran au sein d’une nouvelle chaire industrielle, MACIA, dédiée aux matériaux acoustiques innovants : « Notre objectif est d’optimiser au maximum l’existant tout en explorant des solutions de rupture à l’aide de nouveaux matériaux moins encombrants et plus absorbants comme les métamatériauxFermerEn acoustique, il s’agit de matériaux artificiels dont les propriétés physiques facilitent le contrôle de certaines fréquences sonores. Les sous-marins militaires furtifs furent des pionniers dans l’utilisation de ces matériaux.. Nous étudions aussi la possibilité d’utiliser des matériaux qui transforment le son en électricité pour mieux dissiper le bruit », détaille-t-il.
La glace, ennemie des moteurs
Si nos oreilles sont sensibles au bruit, les moteurs, eux, n’aiment pas le givre. En s’accumulant à l’entrée du réacteur, la glace peut se révéler fatale si des morceaux se détachent et sont aspirés par le moteur. Au risque alors d’endommager sa structure interne, voire d’en provoquer l’arrêt. Ce phénomène de « givrage moteur » est désormais bien compris, mais les outils d’évaluation de la résistance au givrage des appareils demeurent rudimentaires.
Basé au Laboratoire des sciences de l’ingénieur, de l’informatique et de l’imagerie6 (ICube) de Strasbourg, Yannick Hoarau a mis a profit une collaboration avec l’université de Montréal pour apporter une solution innovante à la modélisation des phénomènes de givrage. « Les modèles numériques des industriels ne prennent pas en compte facilement la modification des trajectoires de l’air induites par les couches de glace. Or, les points d’impact des gouttes d’eau qui viennent geler à la paroi dépendent de ces flux d’air qui les transportent », explique-t-il. Dans un article remarqué7, Yannick Hoarau a montré qu’il était possible d’utiliser des approches numériques intégrant naturellement le changement de forme des parois de l’avion à mesure que la glace s’y accumule.
Ces récentes contributions sont autant d’innovations transversales qui seront, à n’en pas douter, au cœur des moteurs de demain.
Lire aussi : « Dans les secrets de la combustion »
- 1. Unité CNRS/CentraleSupélec.
- 2. Centre européen de recherche et de formation avancée en calcul scientifique.
- 3. Institut de mécanique des fluides de Toulouse (CNRS/Univ. Paul-Sabatier/INP Toulouse).
- 4. Unité CNRS/Univ. Jean-Monnet/Univ. Claude-Bernard/École centrale de Lyon/INSA Lyon.
- 5. Unité CNRS/Univ. du Maine/ÉSÉO.
- 6. Unité CNRS/Univ. de Strasbourg/INSA Strasbourg/ÉNGEE Strasbourg/Inria/Télécom ParisTech.
- 7. D. Pena, Y. Hoarau, É. Laurendeau (2016), « A Single Step Ice Accretion Model Using Level-Set Method », Journal of Fluids and Structures, vol. 65, pp. 278-294.
Voir aussi
Auteur
Jean-Baptiste Veyrieras est journaliste scientifique.